TECHNOLOGY
Specification:
- Line speed – 40 mpm
- Minimal speed – 15 mpm
- Strip width – 600 – 1250 mm
- Maximum coil weight – 10 t
- Coil internal diameters – 508; 610 mm
- Maximum external diameter – 1500 mm
- Minimum strip thickness – 0,14 mm
- Maximum strip thickness – 0,80 mm
Color Coating Line Schematic
Whatch the video
Technology
The technological process of coatings application consists of the following stages
- Feedstock threading
- Surface preparation
- Passivation
- Prime coating
- Strip drying after primer coater
- Cooling
- Top coating
- Curing of the strip after application of paint
Feedstock threading
Metal coils are put on two entry coil cars with the help of the bridge crane. Then the cars elevate the coils to load them onto the uncoilers one by one.
Surface preparation
Metal enters the Pretreatment zone before storing in the Entry Accumulator. Strip treatment is performed by means of spray bars rinsing system. The main chemical treatment operations are:
- Degreasing (No. 1 Tank)
- Rinsing
After the pre-treatment zone, the metal goes to the entry accumulator, which is provided for continuous line operation.
Next is the area where the metal surface is prepared. In this area, the strip is processed with spray bars rinsing system.
The main operations of chemical processing of the strip are:
- Degreasing (No.2 Tank)
- Brush scrubbing
- Degreasing (No.3 Tank)
Rinsing tanks No. 2, No.3 – with demineralized water to eliminate solution residues from metal surface.
Passivation
The process is used for applying of complex chemical coating on metal surface with the help of the chemical coater machine to improve anticorrosion characteristics and prime coating adhesion. After that the applied chemical coating is dried.
Prime coating
After chemical treatment strip is directed to the Prime Coater Room, where primer coating is applied to the both sides of the strip in S-wrap primer coater fitted with two double roll units. Each double roll unit consists of a Pick-up Roll to take paint from the tray, and an Applicator Roll to apply paint to metal. The wet film thickness of the primer is to 15 µ (dry film is 6 µ).
Strip drying after primer coater
Metal with a primer coating applied enters the three-zone infrared prime oven, where it is polymerized with the help of infrared radiation. Each zone maintains the certain temperature with the help of a modern automation system. A peak temperature of metal depends on a type of coating. The standard peak temperature is 232 °C.
The oven technology enables to start painting and drying immediately without time loss for oven heating. In contrast, a natural gas furnace requires 45 minutes for heating.
Cooling
After passing the IR-oven a metal strip moves to the water- and air-cooling system where its temperature is lowered from 232°C to 50°C. The cooling tank is manufactured of the stainless steel. Demineralized water is used in this system.
Top coating
Cooled metal is directed to the Finish Coater Room to be top coated. A paint application process is performed by means of U-wrapped finish quick change coater machine with two double rolls units allowing to change color of the top coat without stopping the line, and a coating unit providing application of the back coat. Wet film thickness of standard polyester is 45 µ (dry film thickness is 20 µ).
It is possible to apply other coatings with different film thicknesses while using two or three applicator rolls method.
Curing of the strip after application of paint
Then painted metal is directed to the Finish IR oven, identical to the Prime oven, where it is polymerized.
Cured painted metal goes to the water- and air-cooling system where its temperature is lowered to 50˚C.
Then cooled metal is directed to the Exit Accumulator to maintain continuous operation of the line, afterwards the end of the coil is cut and samples are taken.
Ready painted coil is put on the supports via hydraulic car, and then it is removed to the packing area with the help of a bridge crane.
In the line coil is under a high tension provided by means of five Bridle Stations
Quality
Laboratory
The first independent certificated laboratory in Ukraine was founded with the purpose of carrying out of qualitative analysis of metal and its coating and products standardization.
Our clients will be able to obtain a quality certificate for the products purchased, as well as to request an independent analysis of materials from other suppliers.
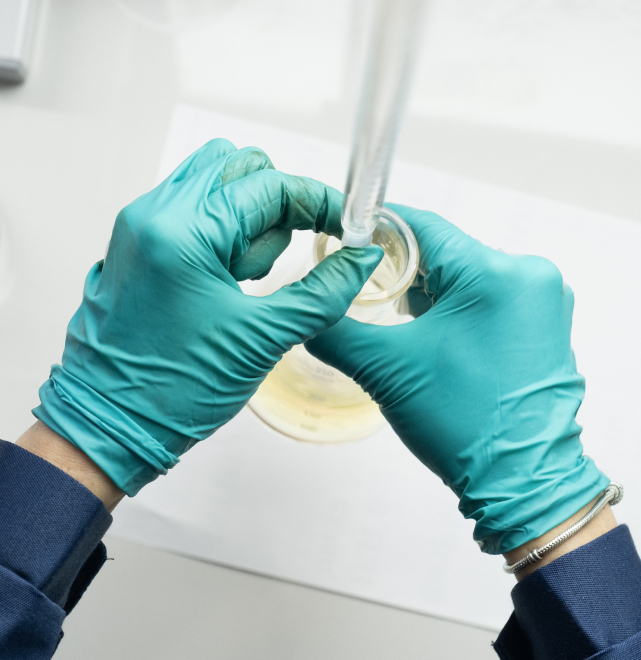
PRODUCTION
Photogallery
Production
Excursions to Production
See for yourself our high standards by visiting our production and seeing the entire process of creating our products.
Contacts
Authorized representative in Europe
DAN-STEEL SP. Z O. O.
45 Fabryczna Street,
Tychy, 43-100, Poland
+48 514 656 655
Production facilities and warehouse
Heavy Metal LLC
50/3 Korabelna Street,
Pervomaysk, Mykolaiv Region, 55210, Ukraine